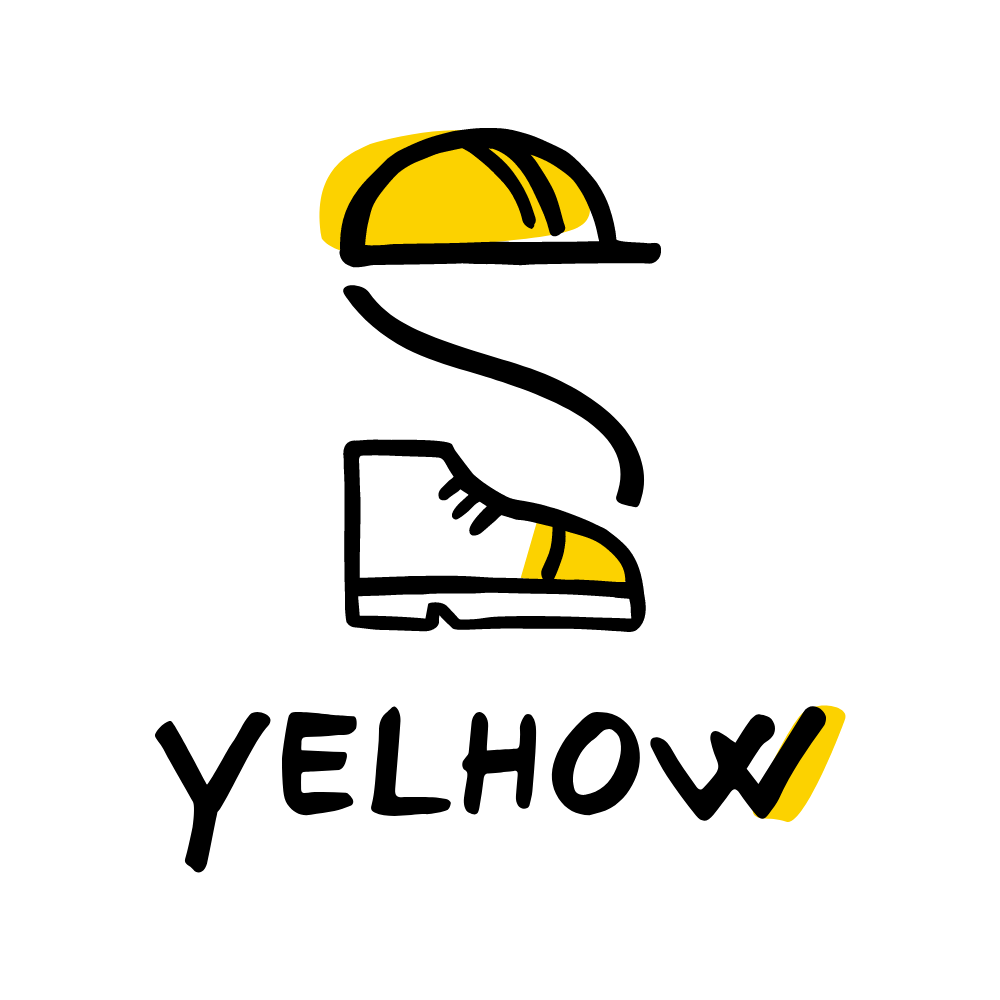
- Homepage
- Our latest news
- The importance of skills in Industry 4.0
The importance of skills in Industry 4.0
Do you have the right people, in the right place, at the right time, in your factory? That's the question posed by Baptiste Gendron, founder and CEO of Yelhow, a software publisher at GI 2024.
In the context of Industry 4.0, the market demands ever more specific and unique products, requiring production lines to constantly reconfigure themselves. To achieve this, it is essential to have men and women capable of reconfiguring these lines and operating the machines.
How to get involved?
“The key is to involve all employees, at all levels of the company, in the overall project. But there's also a technical aspect : it's essential to interconnect with the company's various information systems to integrate the human element into the production flow. This means managing the skills needed to operate the machines and occupy the workstations,” explains Baptiste Gendron, founder and CEO of Yelhow.
He continues, “Involving employees is of course a matter for operators, but also for team leaders, quality managers, methodists, as well as human resources, trainers and tutors, throughout the skills enhancement process. The aim is for them to be able to carry out production operations efficiently.
Connected skills management
On a technical level, we need to connect our solution to human resources management systems to obtain information on employees, temps and absentees,” adds the CEO. Next, we connect to quality management systems to retrieve procedures and operating modes. Finally, we integrate with the ERP and production management system (EMS) to retrieve production plans and check, in real time, that people are authorized to issue production orders”. Yelhow's customer portfolio includes ACC's Gigafactory, Airbus and Accenture.